Powder Metallurgy(P/M)
Powder metallurgy is the conventional forming technique of powder through compaction & sintering, Cold Isostatic Pressing(CIP), and Hot Isostatic Pressing(HIP).

Freedom of design, Flexibility in production
ThetaTech is Instead of purchasing DED and PBF type metal 3D printers from domestic and foreign external companies, we developed them with our own technology through six years of joint research and development with POSTECH . This has secured flexibility and technological independence to stably produce parts according to customer needs without the constraints of commercial equipment . In addition, we are developing next- generation AM methods, FGF and LCM equipment, with our own technology, and we precisely implement difficult-to-cut parts made of titanium alloy, Inconel, and tungsten. We operate the entire process in-house, from material design to printing, sintering, and quality inspection, and provide precision metal 3D printing solutions specialized for the defense, space, and medical industries.
Powder Metallurgy(P/M)
Powder metallurgy is the conventional forming technique of powder through compaction & sintering, Cold Isostatic Pressing(CIP), and Hot Isostatic Pressing(HIP).
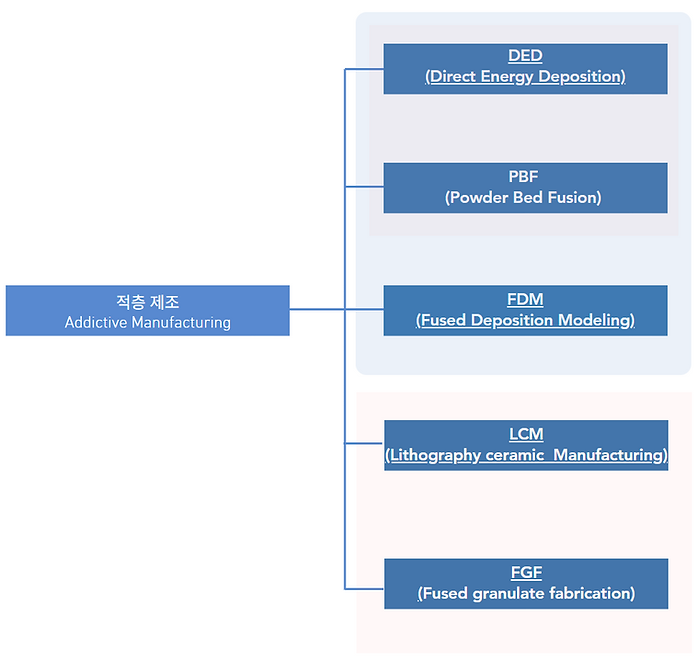
The Future of Metal Additive Manufacturing Designed by ThetaTech
DED (Directed Energy Deposition)
Directly spraying metal powder and melting it with heat source – suitable for manufacturing and repairing large parts
PBF (Powder Bed Fusion)
Selectively irradiating the laser onto a metal powder layer – strength in implementing high-precision and complex shapes
FGF (Fused Granulate Fabrication)
Melt metal pellets with heat and extrude – suitable for low-cost, high-density prototype production, capable of handling heavy materials
LCM (Lithography-based Ceramic/Metal Manufacturing)
Light-curing slurries – enabling ultra-precision parts and metal-ceramic hybrids